Creep-Fatigue Damage Evaluation and Damage Reduction Technology for Heat-Resistant Steels and Alloys used in Thermal Power Plants
In Japan, efforts are being made to reduce thermal power generation and increase the proportion of renewable energy sources, such as solar and wind power, in order to achieve decarbonization. However, it is not possible to completely eliminate thermal power generation. This is because adjusting the output fluctuations of renewable energy sources, which are affected by weather and season, cannot be managed solely by batteries; primarily, thermal power generation must play this role (see Figure 3). In this situation, thermal power plants are forced to operate under load balancing, starting and stopping at intervals ranging from several hours to several days, and such operations are already being carried out.
In load balancing operations of thermal power plants, there is a strong concern that creep-fatigue damage will occur in heat-resistant components, such as headers of the main steam pipes, in addition to creep damage. Furthermore, as the construction of new thermal power plants becomes more difficult, damage evaluation of plants and materials has become an increasingly important issue.
At high temperatures (more than 30% of the melting point in absolute temperature), materials experience time-dependent deformation (creep) even under low stress levels comparable to elastic deformation. While damage to heat-resistant components in thermal power plants mainly occurs due to creep when operating as baseload power sources, load balancing operations that involve repeated start-ups and shutdowns may result in creep-fatigue, which combines both creep and thermal fatigue.
In light of this background, we have started research to investigate the effects of stress fluctuations on the creep deformation of heat-resistant steels (see Figure 4). Additionally, since thermal fatigue is caused by the thermal expansion and contraction of materials, we are also challenging to create and design heat-resistant metallic materials with reduced coefficients of thermal expansion (see Figure 5).
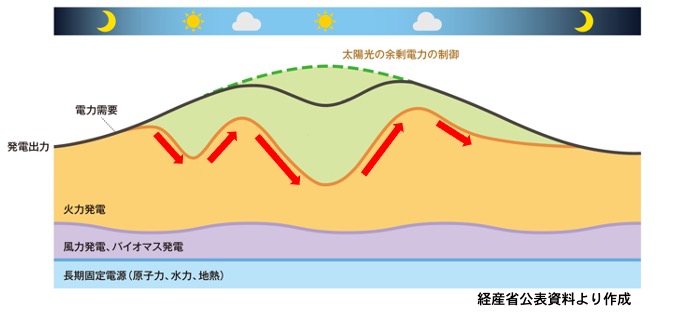
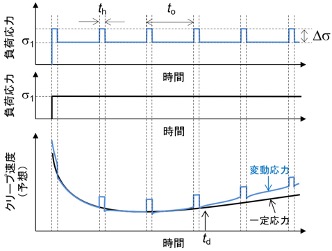
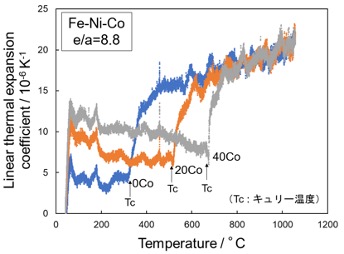